Manufacturing Operations
Gain a competitive edge with manufacturing excellence
by combining proven optimization methods
with digital approaches.
Manufacturing and Operational Excellence
High quality and competitive prices are key factors in keeping up with global competition for producing companies in various industries, like manufacturing, chemicals, or pharma. The target picture: Excellent manufacturing operations well balanced between maximum efficiency and responsiveness to meet customer and value chain requirements enabled by a culture of continuous improvement.
Rely on the depth of our Camelot consulting expertise, which is firmly grounded in extensive operations knowledge. Our consultants not only possess robust industry expertise but also bring invaluable insights gleaned from leadership roles within producing companies. Through our value chain focus, we are positioned to offer a comprehensive, end-to-end perspective. Our manufacturing operations practice at Camelot supports you to transform your operations sustainably – for improved value stream, streamlined production processes and increased value creation.
In today's fast-paced world, businesses are under pressure to continuously refine their operational models, with manufacturing playing a crucial role in this endeavor. Our manufacturing operations practice collaborates closely with clients, drawing on our deep industry experience to drive value and streamline costs every step of the way, from initial identification to implementation.
Patrick Frank, Head of Manufacturing Operations, Camelot Management Consultants
Plant Improvement & OpEx
Transform Your Manufacturing Operations with Our Proven Plant Improvement Approach
Plant improvement initiatives are imperative for manufacturing companies to remain competitive in today’s dynamic market. They ensure operational efficiency, reduce production costs, minimize waste, enhance product quality, and boost overall productivity. By continuously refining processes and investing in technological advancements, companies can meet changing customer demands, maintain profitability, and sustain long-term growth in the fiercely competitive manufacturing landscape. Our Camelot operations consultants guide you every step of the way.
Rapid Plant Improvement
Pressure on manufacturing companies is increasing due to many influencing factors. These include both rising cost pressure and the need to reduce time-to-market. As a result, more short-term measures must be implemented to counteract this. Companies are often faced with the question of where to start. Our scalable rapid plant improvement approach can be applied on single plants as well as multi-plant networks. It allows the quick identification and prioritization of short-term cost and productivity improvement levers in line with a feasible implementation plan to realize short-term value.
Customer-Specific Production System
Many companies currently employ separate stand-alone solutions to enhance productivity within their manufacturing processes. However, the absence of an overarching framework often leads to a lack of cohesion and structure among these individual solutions. To address these challenges, we collaborate with clients to develop a tailored production system that meets specific needs while maintaining standardized elements for structured scaling across various production areas and plants. To expedite implementation, Camelot offers its own production system, which includes basic modules like 5S and lean production, OEE (overall equipment effectiveness), and quick changeover, as well as advanced modules such as line-back logistics, total productive maintenance, and digital manufacturing principles.
Equipment Efficiency / OEE Improvement
OEE (overall equipment effectiveness) is a key lever for reducing costs and increasing productivity in manufacturing. Camelot supports you in collecting data and determining the OEE, as well as drawing the right conclusions from the collected data. We help to categorize and prioritize the actions to improve the OEE so that the right initiatives are launched to address issues such as unplanned equipment downtime, quality defects, or changeover times.
Operational Excellence & Lean
In operations, manufacturing companies grapple with the dual demands of operational efficiency and product quality amid intense market competition. However, outdated production processes and inefficient workflows hinder productivity, leading to bottlenecks, increased lead times, and higher production costs.
With our OPEX (operational excellence) approach, we enable our clients to identify and prioritize necessary levers. Through our guidance we help to sustainably anchor the knowledge in your organization for the long term to establish a culture of continuous improvement.
Operational Risk & Resilience
Companies facing market volatility and supply chain disruptions must manage operational risks and boost resilience. Overdependence on single suppliers, equipment breakdowns, and labor shortages can disrupt production, causing financial losses and reputational harm. Strategies such as diversifying suppliers, preventive maintenance, and employee cross-training help fortify resilience.
Camelot’s rapid risk assessment identifies key opportunities for improvement and enables manufacturing companies to amid uncertainty. In addition, we provide guidance for the development of pro-active and re-active action plans depending on the type of disruption (e.g., natural disaster, strike, or political conflicts).
Success Story: Multi-Plant Performance Assessment and Improvement in Manufacturing
From Operational Excellence Assessment to Implementation of Quick Fixes to Stabilize Operations
Our performance assessment for three plants in Europe and the US, conducted for an automotive tier-1 supplier, allowed us to define, prioritize, and implement improvement measures aimed at quickly stabilizing operations. Additionally, we developed an implementation plan for mid- and long-term improvements.
Within four weeks, 25% of production backlog was reduced. In addition operational dashboards were implemented to make performance more transparent.
Business Process Management & Improvement
Learn How You Can Drive Competitiveness and Business Value Through Seamless Business Processes
Explore short- to long-term approaches aimed at enhancing your process performance and optimizing your process cost base – across functions and company-wide.
Process Cost
Optimization
Companies meticulously explore process optimization opportunities in both Selling, General, and Administrative expenses (S&GA) and Cost of Goods Sold (COGS). In undertaking process cost optimization projects, companies often face three primary challenges: first, identifying the most promising areas for improvement; second, establishing appropriate cost reduction goals; and third, translating potential improvements into tangible results.
Particularly for companies navigating challenging financial circumstances, a swift analysis-to-results approach is imperative to avoid unnecessary expenditures. Camelot offers a proven process cost optimization methodology rooted in business process reengineering. Through this approach, we assess opportunities for process elimination, automation, and outsourcing. Leveraging our extensive experience, we swiftly identify and quantify viable improvement areas and facilitate a rapid implementation focused on achieving quick wins.
Business Process Management & Maturity
Well-organized, transparent, and properly documented processes are fundamental for modern business process orchestration and a major success factor for being competitive. In reality, many companies established functional silos over years, with limited transparency of their activities and potential conflicts between departments (e.g. sales and logistics or planning and production). This circumstance complicates process orchestration to improve process performance and KPI adherence.
We often observe significant process optimization potentials by breaking functional silos and driving supply chain convergence. Structuring process responsibilities clearly, identifying the right levels of process harmonization, selecting suitable IT tool (e.g. process mining), and assessing required process maturity are key elements of introducing business process management in companies. Our broad and project-proven process repository contains detailed processes based on various best practices accelerating process redesign.
Standardized Process Templates
Historically grown process variants are a reality in many companies across all functions. Inefficiencies through complex process execution are part of their daily operations. If companies consider expanding or relocating their business, standardized process templates boost the ramp-up of new locations and simplify process optimization drastically. Especially, if paired with a tailored standard operating procedure (SOP).
Of course, existing locations benefit from process templates, too. It is crucial to understand that process templates do not result in a “one-size-fits-all” approach. It is about having a standardized tool for every job (process variant) and eliminating all unnecessary process variants. This way, companies remain enabled to respond to changing market environments and process requirements. Our broad and project-proven process repository contains exactly that: detailed and SAP-compatible processes based on various best practices to create standardized process templates.
Process Insights & Automation
Continuous process optimization is key to remain competitive and fulfill customers’ demanding needs. However, often companies struggle with finding resources for proper process analysis and with transferring findings to sustainable improvements. Process analyses are often resource-intense due to classical process analysis approaches, like GEMBA, value stream analysis, or process mapping. These approaches are not generally wrong. Their drawback is that they only provide spot analysis, requiring manual effort to identify root cause clusters.
Process mining is a complementing tool that uses transactional data from ERP and connected systems to visualize as-is process performance. Process mining generates insights from spot analyses, but also continuous process monitoring is possible. Learn how your organization can focus scarce resources on process optimization, based on data-driven and automated process analyses.
Success Story: Global Process Template for a CPG Manufacturer
Next-Level Worldwide Process Execution
With the help of our broad and project-proven process repository and vast business process management expertise, we supported a multi-national company harmonizing its processes worldwide. We jointly established a global process template for operations with the ambition to drive process efficiency and automation, strengthen responsiveness to market dynamics and improve operations management capabilities.
Manufacturing Operations Insights
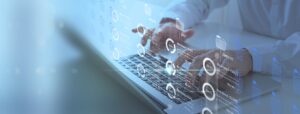
IBP Time Series, IBP Order-Based? What is this?!
Order-Based Planning (OBP), this topic is the current development focus for SAP IBP developments. What is the difference to time series?
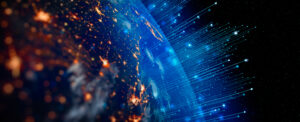
Digital Transformation of Order-to-Cash: What Comes Next?
The digital transformation of order-to-cash is currently on the agenda of many companies as is promises many benefits. But how can these benefits be realized?
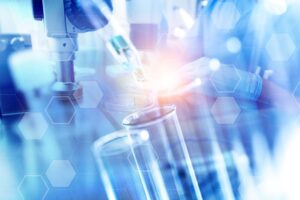
Solving the Flavor Management Problem with the Supply Optimizer
This article shows how we leveraged the capabilities of a market-leading supply optimizer to effectively address the flavor management problem.
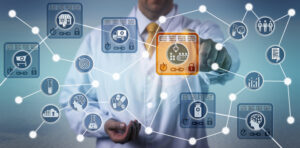
The Top Ten Pharmaceutical Supply Chain Planning Requirements
Learn more about the supply chain planning requirements that companies should implement in a pharmaceutical digital transformation.
Smart Factory
Increasing Your Competitiveness Through Digital Operations and Manufacturing Ecosystems
Digital production is the core to create added value in every area of the smart factory and its value chain. At Camelot, we provide senior leadership with methods and the necessary tools to pragmatically increase performance and efficiency in production through Industry 5.0 principles, ringing in the fifth industrial revolution with AI, advanced robotics, and more.
Digital Production Assessment
Many manufacturing companies find it challenging to accurately assess their digital maturity and capabilities, hindering their ability to chart a path toward greater productivity and efficiency as a smart factory. With Camelot’s “Digital Production Assessment,” businesses can benchmark their current level of digitalization in production operations against best-in-class standards. This serves as a starting point for digital transformation initiatives in manufacturing and process industries.
Manufacturing Technologies & IIoT Solutions for Smart Factories
Numerous companies solely focus on implementing an ERP system as their production solution. However, without closed-loop processes in place, they fail to fully harness the potential for increased efficiency in production. We specialize in guiding companies through the digital transformation process in manufacturing, helping them leverage the benefits of manufacturing technologies across all levels of production, from the edge to company-wide and ecosystem levels. This includes selecting the optimal digital manufacturing solutions for monitoring, controlling, optimizing, and even achieving autonomous operations, along with implementing machine learning and building digital twins.
We also assist in identifying the key value and cost drivers for digital manufacturing, covering everything from connectivity and data mesh to data consumption and data protection, as well as the industrial internet of things (IIoT) landscape. By integrating relevant data both internally and externally into a platform, we enable the development of smart AI-based smart factory applications.
One Step Further: Advanced & Additive Manufacturing Technologies
Industrial automation technology, robotics and additive technologies for manufacturing are advancing rapidly, leaving many companies struggling to keep up and identify the best solutions for their needs. Our continuous market screening enables us to assist in selecting the right automation and robotics technologies to maximize efficiency and profit growth, while minimizing the required investment for your smart factory.
Concept Development for Digital Production Operations & Ecosystems
Modern production concepts in manufacturing involve a combination of production technologies, IT, and human interface. The creation of these comprehensive ecosystems additionally adds complexity for companies. At Camelot, we specialize in developing new digital production concepts tailored to the current level of digital maturity.
This involves selecting the best smart factory use cases to enhance productivity, efficiency, and quality in production, integrating these use cases into a comprehensive plan for seamless expansion within the Industry 5.0 landscape, identifying key levers for an efficient and flexible end-to-end production chain from raw material suppliers to customers, and transforming the company and its ecosystem from solely manufacturing physical products to becoming a data-driven entity with data products integrated along the production chain.
Making Digital Manufacturing Feasible: Transformation Roadmap
Even when a company has a modern production concept in place, there are several hurdles to overcome when transforming into a smart factory. Often, their own capabilities for implementing building blocks are insufficient. We’ll develop a manufacturing transformation roadmap to ensure the sustainable introduction of Industry 5.0, ensuring a smooth implementation of its central components. Additionally, we’ll select suitable cooperation partners for AI, platforms, machine learning, and application development to meet specific requirements.
Circular Manufacturing
Generation of Additional Revenue Streams through Retrieval of Used Products
Increasing raw material and energy prices put pressure on the profitability of operations in the manufacturing industry. Tailored circular manufacturing reduces cost of operations and increases profitability while remaining compliant with an increasing number of ESG-legislations for long-term competitive advantage. Circular manufacturing is part of an overarching strategy to transform towards a green value chain.
Product Portfolio Assessment
Reclaiming used products from end-customers and reusing parts or materials again during manufacturing reduces the amount of used resources and minimizes waste, which is beneficial from an ecological and economic standpoint. Understanding market demand and feasibility of closed-loop manufacturing is crucial to integrate sustainability into your business strategy, while realizing cost saving opportunities at the same time. Another factor is the ease of return of used products, which is simplified by additional service offerings or adapted business models.
Are you wondering which products out of your product portfolio are feasible and reasonable to be returned for value recovery? Benefit from our structured framework to assess your portfolio and to identify the most suitable products out of your portfolio to generate additional revenue streams and appeal to an increasingly sustainability-conscious consumer.
Closed-Loop Supply Chain Design for Circular Manufacturing
To extend a products‘ life cycle, the transportation of used products back to the manufacturer or to the reprocessor, is a prerequisite. The geographical dispersion of used products makes this not as straightforward and efficient as the traditional supply chain. For closed-loop manufacturing, a reversed supply chain that is tailored specifically to product and manufacturer is necessary to reacquire used products from customers, and to close the loop.
By implementing a reversed supply chain, it is important to use synergies with the traditional supply chain and to remain adaptable for additional future needs, to remain competitive and to decrease cost, while meeting long-term sustainability targets. Our experienced consultants can support you along the way to transform towards an efficient and sustainable production, and offer customized solutions for circularity, while remaining compliant with an increasing number of ESG legislations.
Circular Maturity Assessment
Remanufacturing
Extending products‘ lifecycles to enforce sustainable production is increasingly important to present-day companies. Remanufacturing prolongs the usage period of products and decreases the required overall resources for production. It represents the restoration of used products to their former quality level, by exchanging damaged parts, and is an opportunity to generate additional revenue streams. In case a used product is too severely damaged, the remaining parts can also serve as spare parts for more sustainable production.
A thorough analysis of your product’s remanufacturing requirements is crucial to define the specific technical remanufacturing steps and additionally required equipment and tools. Already ingrained “design for remanufacturing ”, through e.g. modularity, standardization, or durability, is a facilitator for remanufacturing and increases the efficiency of the remanufacturing operation. We will help you unlock new business value, by leveraging our extensive manufacturing knowledge and experience.
Looking for Digital Manufacturing Consulting?
Explore our Camelot Digital Manufacturing Services
To excel in today’s competitive market, manufacturing companies require automated, resilient, and integrated processes throughout their value chain. Camelot guides you through a digital manufacturing journey, leveraging SAP technology and digital factory use cases to expedite transformation. Take advantage of our digital services, innovations, and solutions to streamline and enhance your operational processes, optimize resources, and cultivate a culture of continuous improvement.
Camelot Manufacturing Operations Consulting
Camelot’s manufacturing operations consulting ensures sustainable transformation for improved efficiency and responsiveness. Benefit from our deep industry expertise and end-to-end perspective to enhance value creation and meet customer requirements competitively.