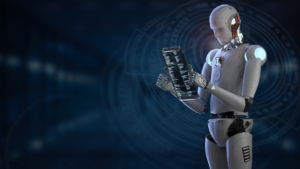
AI-Driven Application & Process Testing: Embracing Agentic Testing
Learn how Agentic AI enables digital transformation, delivering true hyperautomation.
Every supply chain practitioner aspires to achieve integrated planning, smoothly and easily, say naturally. Indeed, this could be realized by means of synchronized applications that automatically relate anyone’s tasks, by propagating relevant data into all IT systems, contributing to the overall company’s material flow efficiency, and – not to forget – to raising a company’s profit.
Is this possible? Actually, yes and no!
Some companies have made extensive investments to be as synchronized as possible, which leans towards a “yes”. Others are still running their supply chain on an interfaced model and decoupled processes which would suggest a “no”.
This article describes how we understand the synchronized planning concept, addressing the necessary frames of reference, providing a picture as clear as possible. Should you wish to extend this thinking with your own feedback, please share it via LinkedIn.
The term “synchronized planning” has been in the focus of software vendors in the SCM field for quite some time now. And even though the concept seems easy to understand, implementing it comes with a lot of work. From the concept perspective, synchronized planning aims at connecting everything, avoiding the tedious and misleading work of reconciliation. This can, for instance, concern reconciling sales and planning domains, reconciling short- and long-term horizon, aligning master data used in execution with those used in tactical planning, linking finance and controlling budget with tactical and operational planning, reconciling IT systems or reconciling solutions.
From the semantic perspective, synchronization should help the propagation of actions based on controlled processing. To some extent, it also refers to real-time integration of systems, or reconciliation of users’ actions.
In other words, synchronized planning is a lot about alignment.
From our point of view, there are four frames of references that we would like to introduce for a better grasp of the synchronized planning concept:
The first frame of reference to consider refers to processes.
Nothing would exist in supply chain management without processes. Thanks to global organizations like APICS, Demand Driven Institute, Tom Wallace, and others, the process aspect of synchronization is well documented. Hundreds of good books explain the focus of each process as well as their connections with the other processes upstream and downstream.
This obviously includes the connection to demand planning, often run on a monthly cycle, with supply planning spinning faster on a weekly basis. Both synchronize with the S&OP process with a monthly or quarterly cycle, linking to the budget process that defines the company vision in practical figures for the following year, on a yearly cycle. All those planning processes possibly feed a business plan (strategic) cycle for the next five to ten years likely based on a yearly cycle. Not to forget that planning connects to detailed scheduling and operations, and therefore to a daily cycle.
On the other hand, connecting two processes comes with many elements. It means exchanging data, sharing aligned master data, and also sharing understanding of those data. For instance, is forecast accuracy the same to all involved stakeholders and functions? Another sensitive example is the selling price considered by OtC (order-to-cash) compared to Controlling breakdown of a price structure, and again compared to a rough estimate for SCM simulations.
Connecting processes also means regular meetings. Are they organized and structured? Are outcomes logged? Are the two processes to be synchronized aligned on the same target? Think of salespeople talking in value, compared to SCM colleagues understanding volumes, both requiring rules to relate volumes and values.
To conclude this first frame, synchronizing processes is a big challenge for companies. It requires breaking silos, which is never ending as they get reconstructed quickly. To be honest, this is theoretically feasible with a strong corporate process governance, with a robust change management and pushing for education as part of the company’s DNA, with people inclusion at all stages.
And to put this high goal into perspective: to me with many years of running SCM projects, I have never seen it all happening in companies. At best, some of the processes mentioned above could smoothly spin together, but usually not to the ideal full sync.
Conclusion: Synchronized planning for processes is still not concluded.
The second frame of reference is the organizational structure of the company related to planning. Here, we look at questions like the limits exposed with silos, induced by diversity of roles, generated by conflicting incentives, etc.
Comparable to processes, hundreds of books describe this desynchronization of internal functions, departments, and organizations, explaining the challenges to overcome so that the company can improve its own performance and market positioning.
There are many synchronization blockers, however, that can illustrate this topic. Let’s consider the simplest organization blocker, which is about the equation that basically states:
Profit equals Revenue minus Cost
On one hand, finance creates the company budget, reducing cost by means of larger production batch hypothesis, reducing year end stock, leveraging possible savings (prioritizing low-cost production rate), focusing on profit balance. In short: what you don’t spend you don’t need to earn. A bit basic but still true. A CFO once told me saving 100 is equivalent to earning 160, with much less investment.
On the other hand, a supply chain department that is exposed to short term variability spins the planning wheel much faster than expected in budget, to get the necessary agility to react to internal and external demand. Under these circumstances, supply chain sometimes calls for smaller batch runs or faster deliveries, to mitigate emergencies. In short, the supply chain preserves sustainability of revenue by maintaining customer service levels, sometimes violating cost, as long as the average profit shown in S&OP reviews is positive and closing gaps to budget by the end of the year.
A supply chain director from the food industry once told me that supply chain is the crossroads of all departments, preventing material flow breakdowns, and often and often receiving the angry calls from different side.
Not only the finance and supply chain departments have a different DNA, also the sales force sees the equation through their own glasses. Profit increases when revenue increases. Pointless to mention the different options used to augment sales revenue like promotion, event, rebates, or monthly end races to match the sales target and get the bonus. I remember a customer selling external inventory without any raised order, to match targets.
The production department is usually closely looking on performance, efficiency, and throughput. Guess what? The equation focuses on cost reduction, optimizing ROI of production assets. I have always heard production as a cost center, never as a profit center.
In conclusion, all four departments taken individually follow their in-built consistent logic, that represents a major desynchronization once considered together. Synchronization of departments is wishful thinking. Beyond this conclusion, maybe, the only moment all departments of a company are well aligned is when the company is still in its start-up phase with full networking, great spirit, and full inclusion of all the pioneers.
The third frame of reference to consider is about the IT landscape including parameters like software solutions, security zones, operational IT constraints, company governance, compliance rules like GDPR, cloud versus on-premises and so many more. These aspects make synchronization a real challenge. Business organizations need more and more connectivity between systems, to support quick decisions. In the recent past with disruptions from Covid-19, a war, or unexpected raw material shortages have demonstrated how important it is to quickly adapt, by getting the freshest synchronized data, regardless of the complexity of technical synchronization efforts.
To illustrate that complexity, let’s take SAP IBP. The new-generation planning software SAP IBP runs in the SAP cloud. It synchronizes with the execution layer sitting in S/4HANA by means of CI-DS (cloud integration for data services) for IBP time series, or SDI (smart data integration) for IBP order-based planning (OBP). SDI / CI-DS ensure bidirectional data exchange between IBP HANA cloud database and the modules for materials management sales and delivery, and production planning. In S/4HANA, data are further synchronized with ePP&DS, hosted in S/4HANA, which covers short- to mid-term production planning optimization, by means on CIF real-time integration. This is not straightforward; however, it works! Software is to gradually evolve and instead of re-coding all software you can connect the modules.
I had the chance to work for several French telecom companies on their APO implementation. Their IT landscape is extremely diversified, because of their history, with hundreds, sometimes even more, of different software applications being either interfaced, or connected, or simply disconnected. Synchronized planning is a major challenge regarding performances and connectivity, which must consider the supplier’s limited supplies (Apple, Samsung, Huawei…) whereas between 500 to 1000 stores must be replenished, every single day, preserving visibility of each individual phone on the shelves, across channels like click & collect, web sales, enterprise sales, shops standard.
You can image the IT system as a physical network filled with liquids that uses many filters, valves, pipes, diameters changes, tanks, to deliver the data to where it is needed.
This IT system frame of reference is, to me, the one that can be clearly addressed, although it still means committing to huge efforts and investments. It is surely not “out of the box” as one can read from time to time.
Our last frame of reference covers solutions, describing what flows into the above-mentioned “liquids network”, where the liquid can be cold or hot, sometimes aggressive, or inactive.
Competing solutions like SAP, Oracle, QAD, Microsoft, do not talk to each other natively via a single software protocol. Supply chain management requires many components like ERP, APS, SRM, CRM, MDM, PLM. To some extent, companies want to select the best-in-class solution for each of those application types, ending with typical situations where SAP S/4 ERP has to connect Salesforce in the cloud, getting the demand plan from FuturMaster on-premises, addressing the tactical plan in SKEP, reconciling demand, supply, and finance in SAP IBP S&OP, whereas detailed scheduling is being made in Ortems, etc…
Furthermore, large organizations with external growth from acquisitions often face the duplication of competing ERP systems or even the same ERP system but with different setups. Obviously, this is a nightmare to synchronization, sounding like a cacophony. Lucky are the small organizations with few IT components; synchronization is part of their central ERP system.
Real-time integration is not possible and neither affordable. The only sensible way forward consists in running daily interfaces, within acceptable design and operation costs.
With all aspects laid out and considering our combined experience over our careers, “synchronized planning” in the sense of real-time data availability is definitely wishful thinking for an actual company.
Business requirements and market transformation will always happen first, followed later by solution evolution to close gaps. Therefore, the paradigm of synchronization is a never-ending story that requires to be constantly addressed by IS/IT organizations with dedicated roles like integration architects, supported by external consulting companies.
Learn how Agentic AI enables digital transformation, delivering true hyperautomation.
Reimagine resilience and proactively minimize supply chain risks
This article shall help you to understand how to optimize your inventory positions in a month – or even less.
Modern PLM systems empower businesses to achieve product excellence in fast-paced markets by enhancing collaboration, agility and innovation.
© Camelot Management Consultants, Part of Accenture
Camelot Management Consultants is the brand name through which the member firms Camelot Management Consultants GmbH, Camelot ITLab GmbH and their local subsidiaries operate and deliver their services.