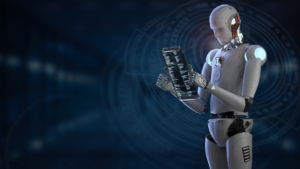
AI-Driven Application & Process Testing: Embracing Agentic Testing
Learn how Agentic AI enables digital transformation, delivering true hyperautomation.
Supply chains in the chemical industry can be grouped into several basic models. These supply chain models are an essential part of the operating model and have a direct impact on business practice.
The future of the chemical industry needs comprehensive digitalization and a change in supply chain management. For the latter, operating models and blueprints play a decisive role. If you are not yet familiar with the concept of operating models, please also consult our article on new concepts for chemical supply chains. But how does such a model come into play?
The determining factors begin with the business model, i.e., the fundamental way in which the respective business segment creates value and earns money derived from customer requirements, and also include the company-specific architecture of value creation (the operating model) and the complexity of the product and customer portfolio.
Theoretically, about 15 individual factors could result in a multitude of combinations and hence models. In practice, however, Camelot considers three basic models to be sufficient – to which two others may be added in exceptional cases.
First, from the five business models for chemical companies used in Camelot, we postulated and roughly described several basic supply chain models – each business model would have to roughly correspond to a supply chain model. Subsequently, we superimposed the supply chains of about 50 real existing chemical businesses from our project history, worked out commonalities, and identified determining factors. We compared the results with our theoretically determined models – in the end, we were left with three to five models that are verifiable in chemical companies, have proven to be robust, and have stood the test of time in consulting practice.
Two of the most common models will be presented as examples:
Commoditized specialty businesses in particular are often sold by larger chemical groups and increasingly find themselves in the hands of financial investors. The holistic realignment of such businesses following a spin-off – whether it be still under the umbrella of its parent company or already for the investor – is a situation in which the lean and flexible model has proved particularly effective in practice. For example, during a carve-out of a pigments business, functional costs were reduced by 5-12%, inventories were lowered, sales potential was identified in a newly defined business segment and structures were streamlined through outsourcing.
Portfolio management in the chemical industry will continue, as mentioned above. This will increase the number of situations in which supply chains have to be transformed under disruptive conditions and investments have to be used in a more targeted manner than before. The need for holistic, model-based improvement concepts is obvious. Defining and designing supply chain blueprints and incorporating knowledge about them into change projects is one task that can be assigned to a group-wide SCM function. In turn, knowledge of specific improvement approaches can be made available at a divisional level to multiple business units with similar requirements. Thus, digital innovations and holistic change concepts will also lead to an upgrade of supply chain management in the chemical industry.
To sum up, we can say that
Learn how Agentic AI enables digital transformation, delivering true hyperautomation.
Reimagine resilience and proactively minimize supply chain risks
This article shall help you to understand how to optimize your inventory positions in a month – or even less.
Modern PLM systems empower businesses to achieve product excellence in fast-paced markets by enhancing collaboration, agility and innovation.
© Camelot Management Consultants, Part of Accenture
Camelot Management Consultants is the brand name through which the member firms Camelot Management Consultants GmbH, Camelot ITLab GmbH and their local subsidiaries operate and deliver their services.