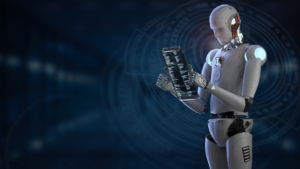
AI-Driven Application & Process Testing: Embracing Agentic Testing
Learn how Agentic AI enables digital transformation, delivering true hyperautomation.
As volatility is here to stay, companies need to structurally embed resilience in their core supply chain decision-making with five capabilities. This requires not only to strengthen the capabilities for effective short-term adjustments, but also to invest in improving strategic preparedness for the unexpected.
Today’s supply chain management is facing severe challenges due to the occurrence of events which are extremely unlikely, and therefore have neither been expected nor sufficiently anticipated by companies across all industries and regions. In fact, the last years have driven many supply chains beyond their tipping point: the global pandemic, geopolitical conflicts, but also the impact of climate change and demographic development have already caused or will cause unexpected long-lasting shortages.
Many, if not most supply chain organizations are therefore still operating in a crisis and risk mitigating mode to overcome supply disruptions, recover and maintain service levels, and to increase robustness across the network. Even those operating supply chain models which have been already adapted to the newly emerged environment will likely be exposed to further changes and challenges.
Firefighting will likely occur less if supply chain organizations are prepared organizationally and in their competences. They will probably be less surprised about the unexpected: an increasing number of companies established dedicated supply chain risk functions and, most importantly, changed the way of managing the network. Resilience-driven decision-making becomes an additional dimension of the supply chain metrics and the organization’s mindset. The new objective is no longer to only minimize costs and capital employed, but rather to achieve the optimal balance between service level, inventory, cost, and resilience. As a result, supply chain teams are more focusing on risk mitigation and resilience to ensure a sustainable supply of products and services.
Based on our experience, it is usually not the right approach to remain in a mindset of “supply chain in crisis” to cope with the current situation as more and better firefighting cannot be the answer. Instead, we need to develop a new structural approach to supply chain decision-making which embeds resilience in every decision we take, to better manage the unexpected on a strategic, tactical, and operational level.
This requires us to rethink and redesign some critical supply chain processes in a systematic way. Not everything needs to change, but some critical capabilities and processes need to be adjusted for more resilience. As outlined in figure 2, supply chain resilience can be enhanced through short-term adjustments and long-term measures, from strategic capacity planning and design to adaptative parametrization and sales & operations execution (S&OE) planning.
The strategic time horizon allows to consider long-term developments and to adapt the company’s supply chain design, planning, and execution accordingly. Dependencies from critical suppliers, logistics services, manufacturing locations and trade barriers can be reduced in a preventive or anticipative manner using a digital network model. The digital network model can quantify the impact of alternative mitigation strategies, e. g., by simulating the expected lost sales and margin. There should be sufficient time to consider and anticipate upcoming regulations, trends and shortages through an end-to-end supply chain planning which includes compliance, capacities and capabilities of external suppliers and services like warehouses or transportation.
For instance, supply chain management is facing an increasing shortage of human resource in logistics and transportation. According to industry associations, the EU is already short of 400,000 heavy goods vehicle drivers. Early impact analysis and adaptation of service contracts, storage locations and transportation lanes can certainly help to remove future logistic bottlenecks as the past confirms. Those clients who anticipated and timely prepared against Brexit-related transportation constraints experienced only minor supply delays.
Moreover, sustainable mitigation of external supply risks should include the design-to-resilience principle: product components and respective vendors are selected as a function of their supply reliability and replace-ability. Consequently, (strategic) sourcing departments must be involved in an early stage of new product development.
On a tactical level, S&OP and Integrated Business Planning (IBP) must have a dedicated focus on demand and supply risks. It takes the economic intelligence of all business functions to detect and consider latest developments and potential (imaginable) events through what-if analytics and scenario-based planning. That is why it is so important that the regularly updated supply chain risk map is not only feeding into the corporate risk management system, but that other units and functions feed risk-related information back into the supply chain risk map.
In addition, a new risk management approach is required to integrate the unexpected in strategic network and capacity planning. Risk management should not solely think in terms of risk events but rather focus on supply chain impact. Instead of assuming potential disrupting incidences, the vulnerability of supply chains should be in focus: companies need to evaluate the impact of disruption scenarios on operations and business results independently of their cause. As a result of this kind of stress testing approach, capacities and parameters along the entire value chain can be adjusted to achieve structural risk preparedness.
Crises and disruptive events are equally affecting (or often originating from) external supply chains and vendors. Since oversight and monitoring of external parties are often limited, the occurrence of potential disruptions is even more difficult to anticipate and to mitigate. Companies need to respond by strengthening two capabilities: a diligent, segmented concept for supplier risk evaluation and intensified supplier collaboration routines.
The evaluation of operational and financial robustness of external service providers and material vendors should include at least key second-tier suppliers. In view of the respective effort and cost, a risk-based supplier segmentation is recommended to limit the number vendors to be checked.
And it is crucial to establish a close and transparent collaboration with suppliers, particularly with critical vendors. Only a fast interchange of information, for instance on supply delays, planned capacities, and demand changes, allows a timely update of supply chain parameters and production plans. Like this, the impact of supply disruptions and demand uncertainty can be minimized through anticipation, planning of buffer and capability for flexible response. Ideally, external vendors and suppliers are subject of S&OP and S&OE planning cycles.
Due to pandemic and geopolitical crises, companies need to cope with extreme demand and supply volatilities. Suppliers cannot meet the contractually agreed service levels so that confirmed delivery dates are being changed on a very short notice. Consequently, supply chain planning and execution is facing the challenge to continuously adapt plans and MRP runs, unless parameters to buffer against volatility are proactively used.
We need to rethink the use of supply chain stock parameters for such a highly volatile situation. Parametrization needs to provide the right level of risk buffers against volatility (like a risk/ insurance premium). This is not a static process: where volatility is increasing, buffers need to be timely adjusted. Thus, a fast, frequent, automatic, and rules-based adjustment of supply chain parameters like lead times and inventory levels across all material types and BOM components is a key prerequisite for ensuring sufficient service level and customer satisfaction. Relying on manual, slow adjustment of key parameters will not be sufficient.
Here, evidence-driven supply chain analytics, for instance applied to material movement and BOM data, can immediately reveal the appropriate planning values of safety stock and lead time parameters across multi-stage production and supply network.
Neither the granularity nor the frequency of tactical S&OP or IBP will be sufficient to manage unexpected events. Supply chain management in times of pandemic and geopolitical crisis requires faster action on a daily and more detailed level to adjust within supply lead times or operational horizons. That is why S&OE is of increasing importance to successfully steer supply networks in volatile and uncertain environments. Unexpected demands and supply events can be timely detected and controlled through an effective S&OE process supported by real-time data and respective reporting, as outlined in figure 3.
A distinct (weekly) S&OE process can ensure the execution of S&OP plans by breaking down the tactical input from S&OP into detailed instructions that can be executed in daily business. S&OE links tactical and operational planning and therefore enables response to deviations between the planning horizons (and frequencies). Given sufficient monitoring capability, S&OE safeguards against demand and supply fluctuations in the operational horizon (e.g., zero to three months) and allows timely reaction to major changes in demand or supply.
We conclude that SCM leaders need to calibrate their expectations on the business environment. Markets are not likely to return to their initial state. Instead, continuous adaptation is required to mitigate supply chain disruption. Managing the unexpected becomes a day-to-day challenge of supply chain managers who can operate naturally in an environment of high volatility and unexpected events, if a risk-aware supply chain organization, a highly adaptive supply chain design, supply chain planning that includes commercial environment data, and close supplier collaboration have been established.
Learn how Agentic AI enables digital transformation, delivering true hyperautomation.
Reimagine resilience and proactively minimize supply chain risks
This article shall help you to understand how to optimize your inventory positions in a month – or even less.
Modern PLM systems empower businesses to achieve product excellence in fast-paced markets by enhancing collaboration, agility and innovation.
© Camelot Management Consultants, Part of Accenture
Camelot Management Consultants is the brand name through which the member firms Camelot Management Consultants GmbH, Camelot ITLab GmbH and their local subsidiaries operate and deliver their services.